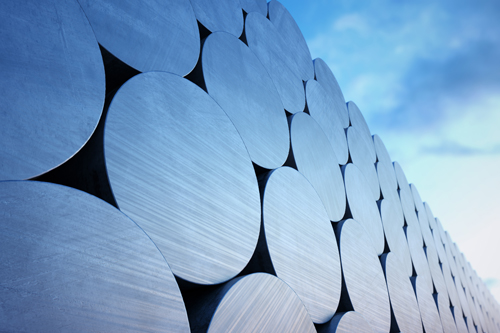
The world’s second most used metal after steel, aluminium is blessed with a host of positive characteristics that have made its use invaluable to the modern world. The most common metal found in the earth’s crust, it possesses a remarkably low weight-to-strength ratio, high resistance to corrosion, is easy to shape and is 100 percent recyclable.
Despite aluminium’s importance to several multi-billion dollar sectors, including the aerospace, transportation, medical and construction industries, surprisingly there remain only a handful of integrated aluminium producers in existence today. One of the elite few is Turkey’s Eti Aluminyum.
Eti Aluminyum was originally established in 1962 by the Turkish government, with 15 years passing before it reached full capacity production in 1977. More recently the company embarked on a transition into the private sector when it was acquired in 2005 by the Turkish construction, energy and mining group Cengiz Holding. This event kick started a comprehensive modernization process for the company, one that continues to this day.
Eti Aluminyum is Turkey’s only producer of liquid aluminium and it is the country’s only fully integrated producer which takes in untreated ore downstream and then has the capacity to fulfil every process requirement to the finished product. The company has its own bauxite ore mines located just 20 kilometres away from the factory and this is the starting point of its operations—the chemistry of aluminium means it is always found combined in other minerals, most frequently bauxite ore.
Using the technology of today there are two primary ways of producing aluminium, the first being from ore, creating what is known as primary aluminium, and the other being from scrap, creating secondary aluminium. Eti Aluminyum’s Seydi┼ƒehir Aluminium Plant, located in the Central Anatolia region of Turkey, is an integrated primary aluminium production plant. From here the company is able to convert aluminium ore into metallic aluminium by first processing the ore and then shaping it through the use of casting, rolling and extrusion systems.
The integrated production process itself consists of five main production phases. These are bauxite mining, aluminium production, liquid aluminium production, the alloying and casting of the liquid aluminium, and the last but by no means least, the production of semi and/or end products through the use of the aforementioned casting, rolling and extrusion processes.
Today Eti Aluminyum provides employment for more than 1,300 individuals, while its plant possesses the capacity to process some 460,000 tonnes of bauxite ore each year and 60,000 tons of aluminium per annum. There is also an on-site casting facility with a capacity of 75,000 tons a year. Eti Aluminyum produces primary and cast aluminium products as well as wet and dry aluminium hydroxide, calcined alumina and a small quantity of high Mg-alloyed plates. In addition, the company’s facilities are also equipped to handle the production and commercial sale of aluminium hydrate, alumina, and aluminium sulphate and vanadium sludge.
The aluminium hydroxide product is used by aluminium sulphate, poly aluminium chloride (PAC), zeolite and other special hydrate producers. The metallurgical alumina product is used mainly by the smelter department internally, as well as by refractory, ceramic and other special alumina producers. The casting products consist of re-melt ingot, alloyed and non-alloyed ingots, billets and slabs. Here, re-melt ingots are used by billet and slab producers while the alloyed and non-alloyed ingots are used by piston producers, cable manufacturers, etc. Billets are used by extrusion producers and slabs are used internally by the rolling plant. Meanwhile, the high Mg-alloyed plates that the plant produces are typically used by machinery builders, ship builders and the defence industry.
Since its privatisation, modernising the legacy of Eti Aluminyum’s plant and related facilities has been a key priority. While its existing infrastructure has undoubtedly served the company well for almost 40 years, a comprehensive upgrade was nevertheless of paramount importance if it was to be able to increase equipment and process efficiency, plant productive, improve work conditions and safety, and reduce emissions.
Making all of this a reality was always going to be quite the challenge and it is one that the company is continuing to face up to as we enter 2014. As well as upgrading all of the equipment and infrastructure relating to its two methods of aluminium production, machinery used throughout Eti Aluminyum’s operations is being systematically brought into line with new technology and regulations, while great progress continues to be made towards the construction of a new coal powered steam boiler plant and the installation of a more modern smelter. Both the latter undertakings are expected to be completed in 2014.
Eti Aluminyum’s Seydi┼ƒehir Aluminium Plant is estimated to be responsible for meeting around 15 percent of Turkey’s annual aluminium demand. Therefore it stands to reason that many within the country are waiting excitedly for the company’s modernisation plans to bring about an increase in its plant’s production output from 60,000 to 75,000 tonnes of aluminium by early 2014, a target that appears well within its reach.
Written by Will Daynes, research by Abi Abagun